数字化和物联网如何
塑造未来的车房
数字化和物联网 (IoT) 的融合将为各行各业的工业生产商开创一个新纪元,尤其是眼镜光学行业中的单件流批量生产。为了通过技术打造未来的车房,必须了解这些技术优势以及车房需要如何去适应。
如果我们有一台计算机,它可以利用自己收集的数据了解事物的一切,而无需我们的任何帮助,那么我们就可以跟踪和计算一切,从而大大减少浪费、损失和成本。我们将知道何时需要更换、维修或召回物品,以及这些物品是新鲜的,还是已经过了最佳使用期。
Kevin Ashton于1999年创造了物联网一词(通过Dataversity)。
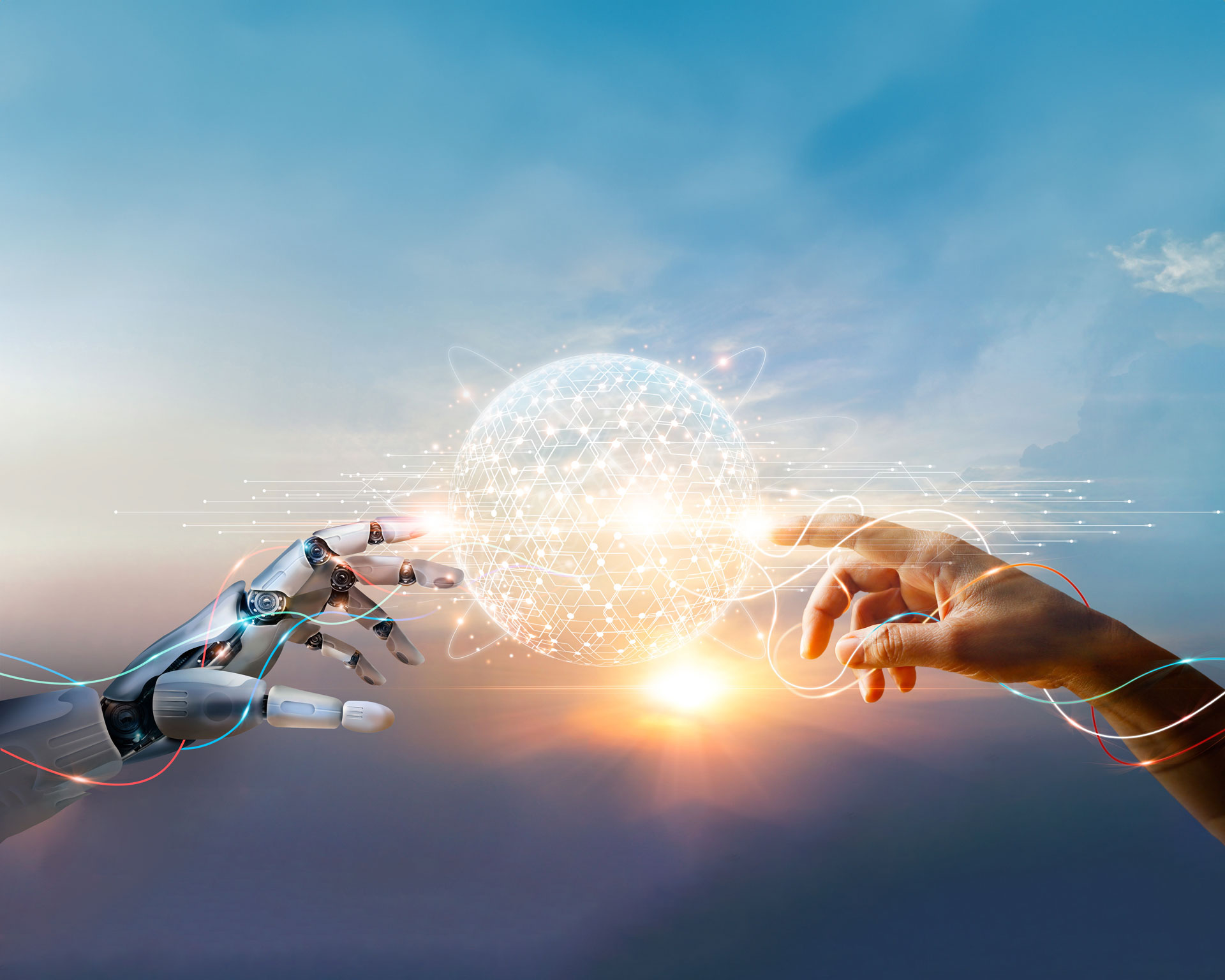
物联网
物联网描述的是一种互联的数字环境,在这种环境中,设备相互连接并共享数据。这一术语是在1999年被创造出来的,而物联网的实际使用最早可追溯到1980年,我们今天所知的物联网与智能技术的兴起息息相关。
物联网和工业4.0
在打造未来车房的背景下,物联网 (IoT) 在实现工业4.0的愿景方面发挥着举足轻重的作用。工业4.0通常被称为第四次工业革命,它代表着一种转变,即数字技术和自动化无缝集成到工业流程中,从而产生智能工厂的概念。工业4.0的核心是利用人工智能 (AI)、大数据和物联网的力量来提高效率,实现灵活且反应迅速的生产。
在工业领域,物联网传感器和设备是收集机器和设备实时数据不可或缺的工具。这些数据为明智决策、预测性维护调度、流程优化和提高整体运营效率奠定了基础。从本质上讲,物联网不仅提供了必要的数据,而且还提供了工业4.0所必需的连接性,从而彻底改变了传统制造业,建立了一个更加互联、自动化和高效的生态系统。
在智能技术出现之前,互联网仅限于平板电脑、智能手机、计算机和笔记本电脑。然而,数字化使智能机器得以崛起,它们可以相互连接,以便与用户共享数据,让用户深入了解设备是如何工作的。物联网促进了数据驱动的生产,实时数据可以轻松共享。
目前,人工智能的使用率正在上升,一项研究显示,三分之一的IT专业人士已经在利用人工智能来实现各种机器流程的自动化。
该研究还指出,在全球范围内,34%的企业已经采用了人工智能,这凸显了人工智能在现代工业中日益增长的重要性。
在物联网的推动下,数据驱动型生产已准备好在塑造制造业的未来中发挥关键作用。它需要生成和垂直共享实时数据,促进数据科学家和生产专家之间的密切合作,以实现人工智能应用。要推动车房进入这个数据驱动的未来,有四个需要考虑的关键因素。
IT系统架构需要调整
虽然目前许多生产线都连接到互联网以执行上传客户数据等任务,但其连接性往往受到所使用协议的限制。那么,IT系统如何发展才能应对这一挑战呢?一个潜在的解决方案是将IT系统基础设施过渡到一个植根于网络技术的标准化架构,该架构可容纳所有设备,从而释放出最大的生产力。
要成功实现这一转变,建立正确的协议至关重要,这些协议应有助于建立强大的连接,实现从机器到云的纵向无缝数据传输和处理能力,以及机器之间的横向无缝数据传输和处理能力。这种级别的连接使操作员能够实时了解生产线的情况。例如,他们只需点击一下屏幕,就能访问远处机器的状态快照、诊断错误并做出明智决策。遗憾的是,如果不对基础设施进行调整,要实现这种级别的连接仍然遥不可及。未来车房的实现取决于IT系统架构的适应性。
要充分利用数据驱动型生产所带来的机遇,必须从调整IT架构开始。
然而,这一趋势有一个明显的例外 - 打印机。
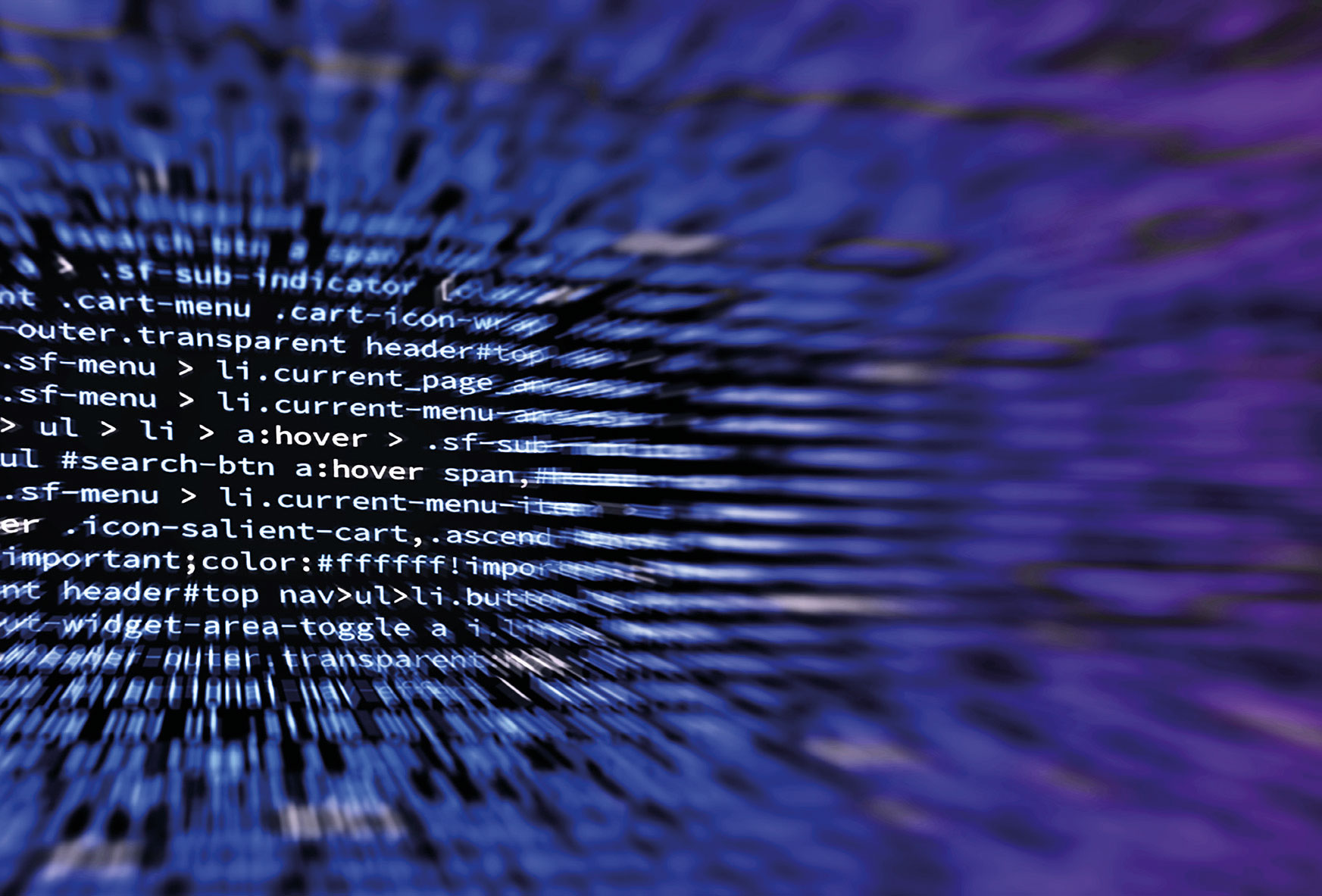
数字化推动可持续发展
近年来,随着创新和技术进步的不断推进,许多二十多年前的技术已经过时。
一些车房努力向无纸化操作过渡,但这些努力往往因缺乏人体工程学设计、无法无缝集成人工流程以及不合格的人机交互而失败。
然而,随着物联网(IoT)时代的到来,无纸化车房的梦想不仅变得更加可行,而且效率和用户友好性也显著提高。Satisloh的尖端无纸化技术结合了电子墨水、WiFi、NFC(近场通信)和RFID(射频识别)技术,可在屏幕上无缝显示关键信息,形成电子工单。
这种基于简单技术的创新可以真正取代纸张,尤其是在所有手工流程步骤中,例如镜片分批,为操作员提供清晰的指引,让他们知道哪个镜片属于哪个位置 -
无纸化技术的优势不仅体现在效率和可行性上,还有助于保护宝贵的自然资源。通过减少对墨粉和纸张的需求,无纸化解决方案在保护环境方面发挥了关键作用。
这只是采用数字化和物联网所带来的环境效益的一个例子。
据《福布斯》报道,物联网设备能够执行更多的功能,从而消耗更少的能源,使其更加环保。物联网设备还可通过优化减少能源消耗,并使用低功耗或替代能源。
如果使用得当,人工智能将创造效益
目前,在技术领域使用人工智能是一个大趋势,已有许多使用案例。这一变革浪潮产生了许多实际应用,例如在IT行业利用人工智能进行反病毒软件开发和部署等任务。
随着当今技术的不断进步,人工智能算法的多功能性已达到一定水平,使其能够胜任各种任务。在眼镜光学行业,这将转化为对机器进行高精度训练的能力,使它们能够非常准确地识别划痕或光学像差等瑕疵。
此外,通过实施人工智能驱动的预测性维护和异常检测系统,机器可以减少停机时间并提高运行效率。它们可以预测何时需要维护或部件何时可能出现故障,从而避免意外的生产中断。
人工智能的模式识别能力在提高产品质量方面发挥着至关重要的作用。
它可以分析机器条件和生产流程中的复杂模式,并将其与最终产品的质量联系起来。例如,人工智能可以监控主轴在镜片切割过程中使用的电流,从而确保精度和一致性。
此外,人工智能的图像识别能力使机器能够自主执行质量控制任务,检测最终产品外观中的缺陷或变化。从本质上讲,人工智能不仅能简化操作,还能提高眼镜光学产品的整体质量和一致性,从而有可能彻底改变镜片生产。
智能供应:参与最终执行的直观软件
如今,许多行业在订购和管理零件和耗材时仍然采用传统的、被动的方法。这种方法通常需要费人工的手动操作,例如确定何时需要新零件、创建发票以及与客户协调以了解其需求。虽然这种方法仍能发挥作用,但其效率还有待提高。车房所有者必须找到一种高效的方法。
然而,现在有一个触手可及的变革性解决方案:
利用云计算和系统来实现整个流程的自动化,可以显著提高效率和成本效益。
未来将不再依赖单向订单和运输,而是由机器直接产生对所需零部件和耗材的需求。然后,这些部件和耗材会准确地送到需要的地方,就在机器旁边。
这种方法省去了人工操作步骤,并确保了所需部件随时可用。平板电脑的引入进一步简化了流程,使供应管理变得像轻点一下鼠标一样简单。
例如,如果在生产线上增加一台机器以提高产量,则无需对员工进行密集培训或手动调整。一切都将自动完成,从而显著降低成本,提高运行效率。
此外,通过利用尖端的物联网技术,我们可以通过提高对何时订购新部件的识别能力来进一步增强这一自动化系统。
这不仅能提高效率,还能确保在工作流程中无缝集成新机器,而无需采购额外部件。其结果是,生产流程更加灵活、更具成本效益和效率,为未来的生产做好准备。
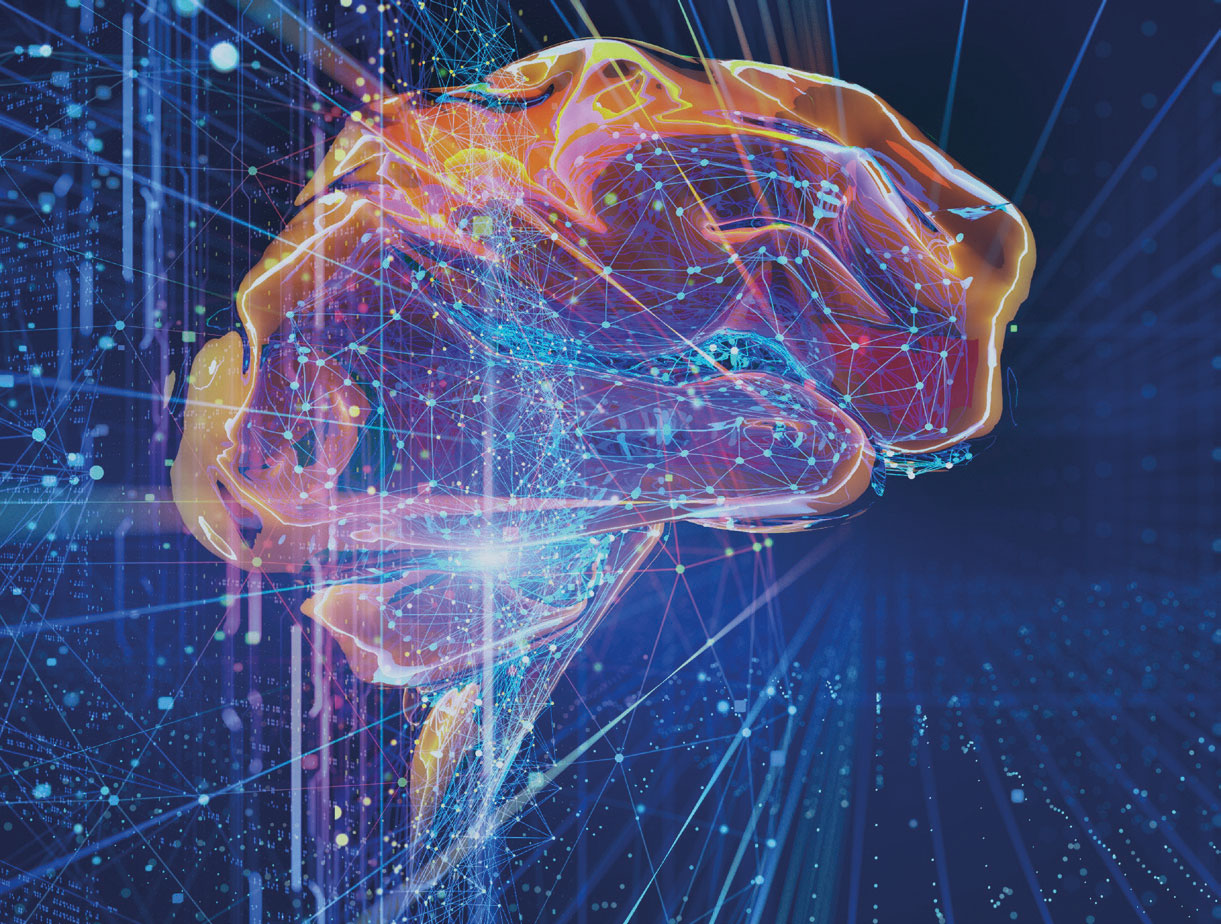
效率是这一转变的核心。
拥抱未来的车房
数字化和物联网 (IoT) 的快速发展将彻底改变车房,尤其是眼镜光学行业的车房。这一变革的驱动力是追求更高的效率、大幅节约成本,以及从根本上改变我们的质量控制和生产流程。
物联网、数字化和自动化的整合通过减少人工操作步骤和优化资源配置来简化操作。因此,镜片生产的效率大大提高,使车房能够更轻松地满足不断增长的需求。
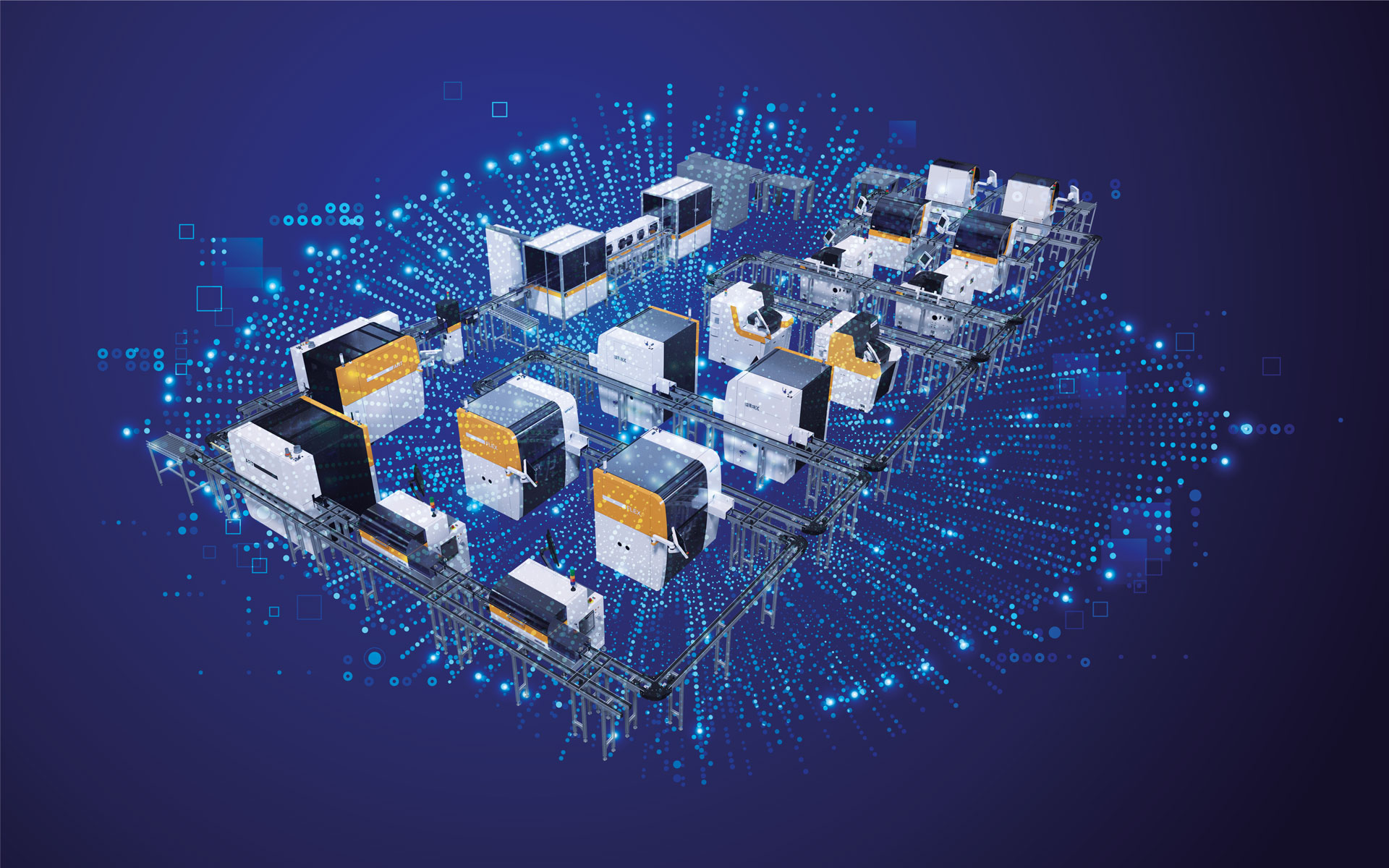
此外,大量节约成本也是采用这些技术的一个重要成果。预测性维护、供应管理自动化和生产精确化都有助于降低运营成本。这使车房能够更有效地分配资源,投资于进一步的创新,并保持在眼镜光学行业的竞争力。
就眼镜光学行业而言,这些进步将对依赖机器生产镜片的车房产生深远影响。它们将能更好地满足日益增长的定制镜片需求,降低生产成本,并确保眼镜质量达到最高标准。随着眼镜店适应并接受这些技术,它们将在这个时代茁壮成长,未来的眼镜店将不仅仅是一个愿景,而是一个实实在在的现实,提供更好的眼镜和更好的用户体验。
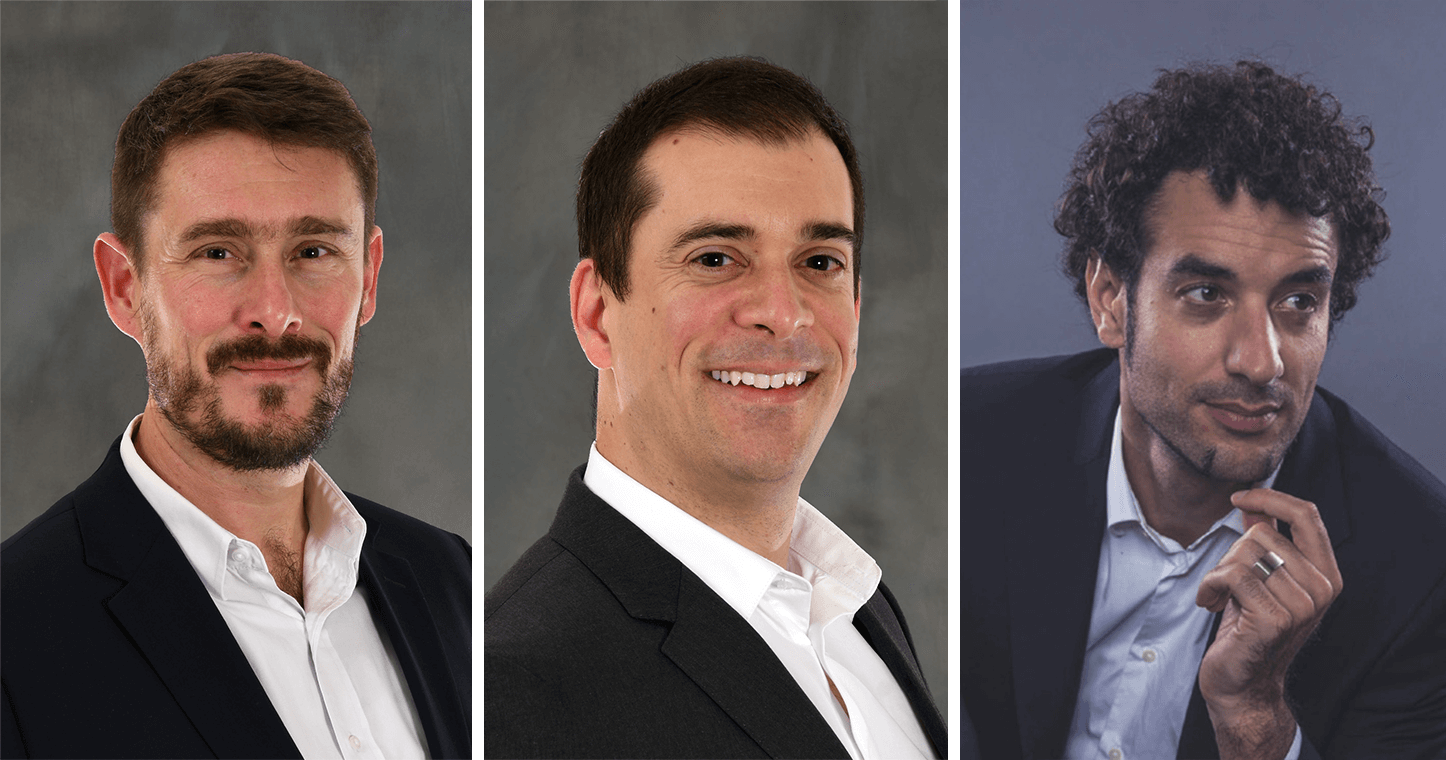
文章作者:
Michael Krei博士
Satisloh集团全球研发副总裁
Xavier Bultez
Satisloh集团集成解决方案副总裁
文章撰稿人:
Sven J. Koerner博士
NLP/NLU/AI研究员