La voie vers une production de verres durable et rentable
Répondre aux besoins du présent sans compromettre la capacité des générations futures à répondre à leurs propres besoins.¹
La durabilité comprend non seulement l'examen de l'impact environnemental de la production, mais aussi trois autres piliers pondérés de manière égale : les facteurs économiques, environnementaux et sociaux. C'est pourquoi il est essentiel de trouver des moyens permettant aux fabricants de produire à des prix compétitifs des produits qui répondent aux besoins humains et améliorent la qualité de vie tout en réduisant progressivement les dommages causés à l'environnement.
¹ Assemblée générale des Nations unies (1987) Rapport de la Commission mondiale sur l'environnement et le développement : Notre avenir à tous.
L'éco-efficacité est l'un des principaux outils permettant de promouvoir une transformation vers la durabilité. Elle est obtenue en réduisant progressivement les incidences sur l'environnement et l'utilisation des ressources tout au long du cycle de vie du produit jusqu’à un niveau ne dépassant pas ce que la planète Terre est capable de donner.
La production industrielle est sans aucun doute l'une des plus grandes consommatrices de ressources.
Il ne fait aucun doute que la production industrielle est l'une des plus grandes consommatrices de ressources. Selon le Rapport mondial sur la mise en valeur des ressources en eau 2019 des Nations unies, 40 % de toute l'eau douce en Europe est utilisée pour la production industrielle et énergétique - 20 % dans le monde entier. La production industrielle est donc la deuxième plus grande consommatrice après l'agriculture. Pour améliorer l'éco-efficacité dans la fabrication des verres, il est essentiel de minimiser la quantité de déchets dangereux, d'eau et d'énergie par verre produit.
En produisant environ 600 millions de verres par an, les Rx Labs créent environ 40 000 tonnes de copeaux, utilisent 4 800 000 m³ d'eau douce et 1 800 MWh d'énergie électrique. Pour mettre les choses en perspective, la quantité de copeaux représente presque quatre fois le poids de la Tour Eiffel, tandis que l'eau peut remplir environ 2 000 piscines olympiques et que la quantité d'énergie pourrait alimenter tout Paris pendant un mois. En outre, ces chiffres ne tiennent même pas compte de la production semi-finie, de la logistique et des autres étapes du cycle de vie global du produit.
En examinant comment les technologies nouvelles et vertes, les machines intelligentes et l'internet des objets (IdO) permettent la durabilité 4.0 grâce à une fabrication éco-efficace, nous constatons que la réduction de l'empreinte environnementale par l'utilisation de moins de matériaux physiques et de ressources naturelles contribue à une production durable de verres. En outre, l'utilisation continue d'alliages dans la production ophtalmique exploite des matériaux précieux et libère des résidus toxiques dans l'environnement, ce qui rend sa réduction particulièrement souhaitable.
La production de verres de contact est une activité à part entière de la société.
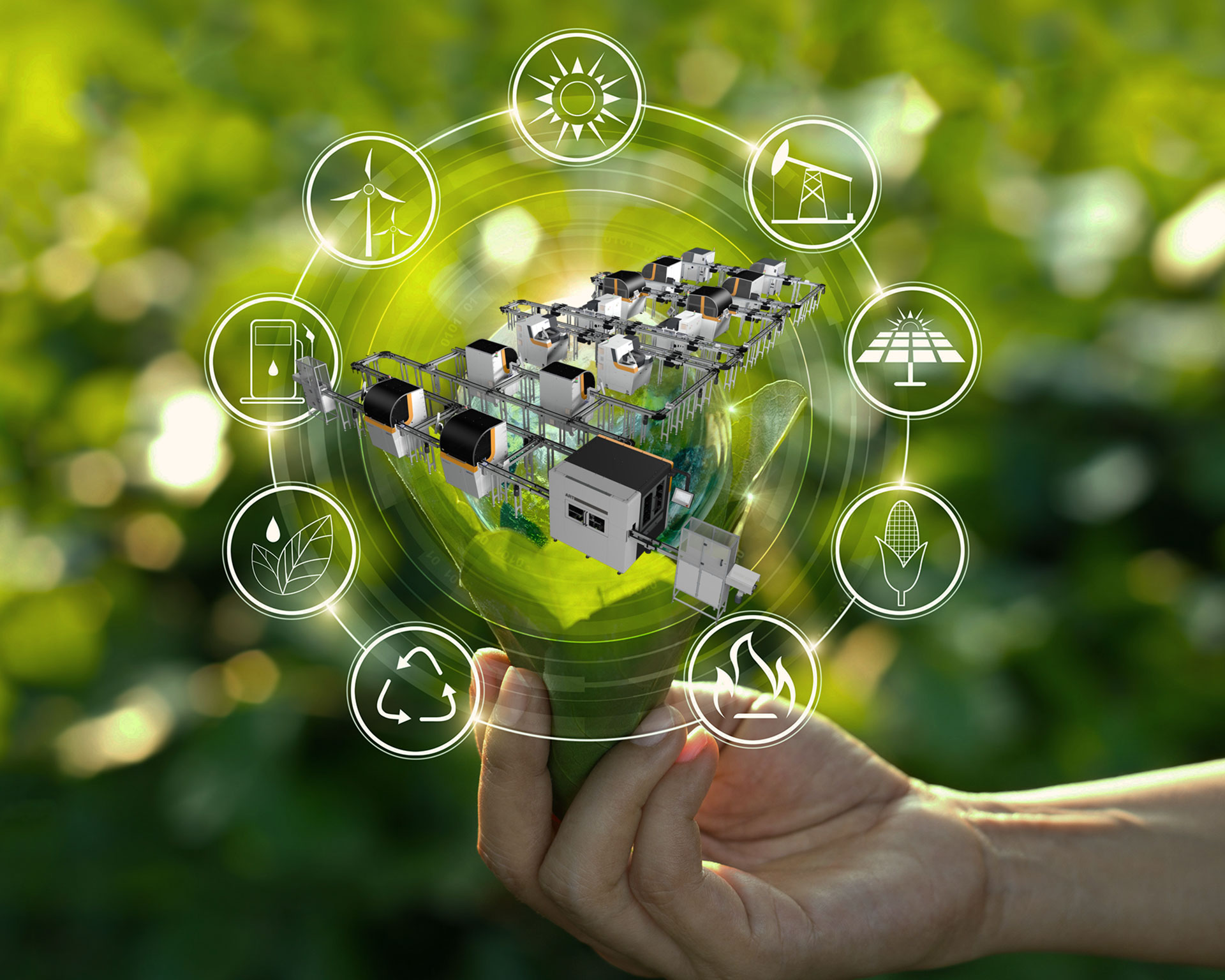
La fixation d'objectifs : L'éco-efficacité n'est pas seulement la protection de l'environnement, mais aussi la production de produits à des prix compétitifs tout en minimisant l'impact sur l'environnement - la fixation d'objectifs est donc d'une importance cruciale.
Les entreprises cotées en bourse de tous les secteurs utilisent le développement durable et l'éco-efficacité comme des avantages concurrentiels majeurs. Essilor affiche sur sa page web des objectifs de réduction de l'intensité de l'eau de 20 % et de l'intensité de l'énergie de 15 % par rapport à une base de référence de 2015. Zeiss a récemment annoncé qu'il deviendrait neutre en carbone à l'échelle mondiale d'ici 2025.
Pour atteindre des objectifs ambitieux, les laboratoires doivent se rappeler que la ferraille est un double déchet, et qu'il est donc utile d'augmenter le rendement autant que possible, ainsi que d'utiliser des équipements de dernière génération. Les technologies de remplacement des alliages permettent de réduire facilement les émissions de substances toxiques à zéro, ce qui constitue une autre occasion de réduire l'empreinte environnementale de la production de verres.
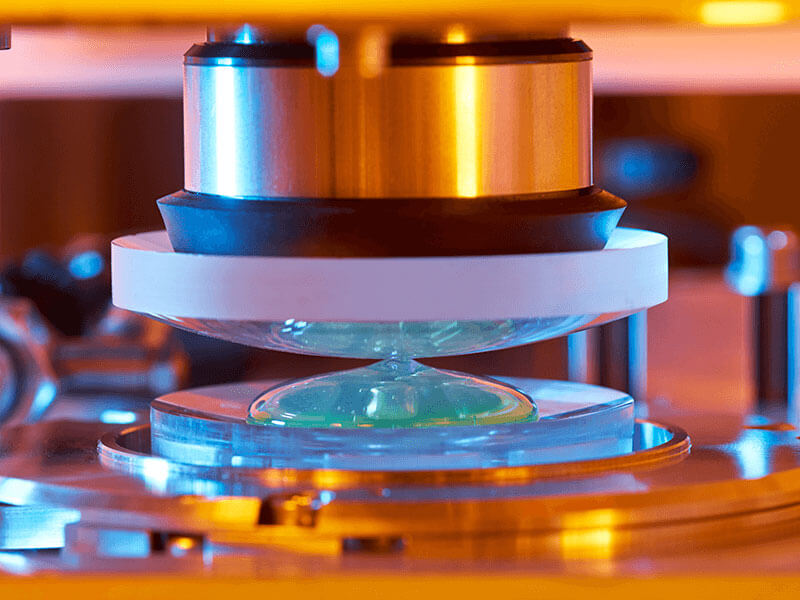
Minimiser les substances dangereuses grâce à ART
L'analyse du cycle de vie (ACV) réalisée à l'aide d'une étude simplifiée inspirée des normes ISO 14040/14044 montre que ce n'est pas l'eau ou l'énergie, mais les substances dangereuses rejetées dans l'environnement à la suite de l'utilisation d'un alliage qui sont les plus grands coupables. La concentration de cadmium dans l'alliage peut être 40 fois supérieure à celle autorisée pour les eaux usées. Selon les calculs de l'ACV, l'impact environnemental des restes d'alliage est 60 fois plus élevé que celui des déchets, de l'eau et de l'énergie.
Le blocage des verres avec ART offre une alternative respectueuse de l'environnement au blocage traditionnel des alliages.
Depuis l'introduction de la technologie ART (Alloy Replacement Technology) jusqu'en juin 2020, elle a permis d'économiser environ 37 400 kg d'alliage qui se retrouvent dans les copeaux et les eaux usées (en supposant que pour chaque lentille bloquée en alliage, la perte d'alliage est en moyenne de 0,4 gramme). Environ 5 % de l'alliage est du cadmium pur, de sorte que la réduction de l'utilisation de l'alliage, combinée à la réduction de la consommation d'énergie et à la diminution des déchets et de l'eau dans la production de lentilles, réduira considérablement la pression exercée sur les ressources naturelles de la Terre.
Les machines ART constituent la prochaine génération d'équipements qui aideront les laboratoires à évoluer vers une production éco-efficace. Grâce à l'arrangement ART-Blocker/Deblocker, les laboratoires verront leur consommation d'énergie réduite de 50 % par rapport aux quatre équipements dont l'alliage a besoin. En outre, les machines ART n'ont pas de chauffage de réservoir d'alliage ni de plaque de refroidissement, ce qui signifie une consommation d'énergie encore plus faible.
L'ajout d'un système de filtration de l'eau à l'appareil de déblocage recycle l'eau dans le système, réduisant ainsi la consommation d'eau jusqu'à 80 %. Enfin, les émissions de plomb et de cadmium toxiques sont réduites de 99,99 % et il n'y a pas de microplastiques en raison de l'élimination du ruban adhésif de protection des surfaces dans le processus ART.
Gérer les déchets de copeaux
Les déchets plastiques sont un problème mondial ; les copeaux, la ferraille et le carton représentent plus de 50 % des déchets dans la fabrication des verres. Seul le polycarbonate pur faiblement contaminé peut être recyclé, la réutilisation des polymères thermodurcissables (CR39 et Hi-Index) n'étant possible que dans une certaine mesure. Ramener les copeaux de la machine dans le circuit de recyclage peut être un défi, et séparer les copeaux après avoir traité un mélange de matériaux dans une machine est encore plus difficile. Les éléments suivants permettent de recycler les copeaux:
- Traitement séparé
- Briquetage pour un recyclage plus facile et moins de perte de liquide de refroidissement
-
Recyclage des thermoplastiques comme le polycarbonate
-
Réutilisation des polymères thermodurcissables comme le CR39 pour des applications spécifiques
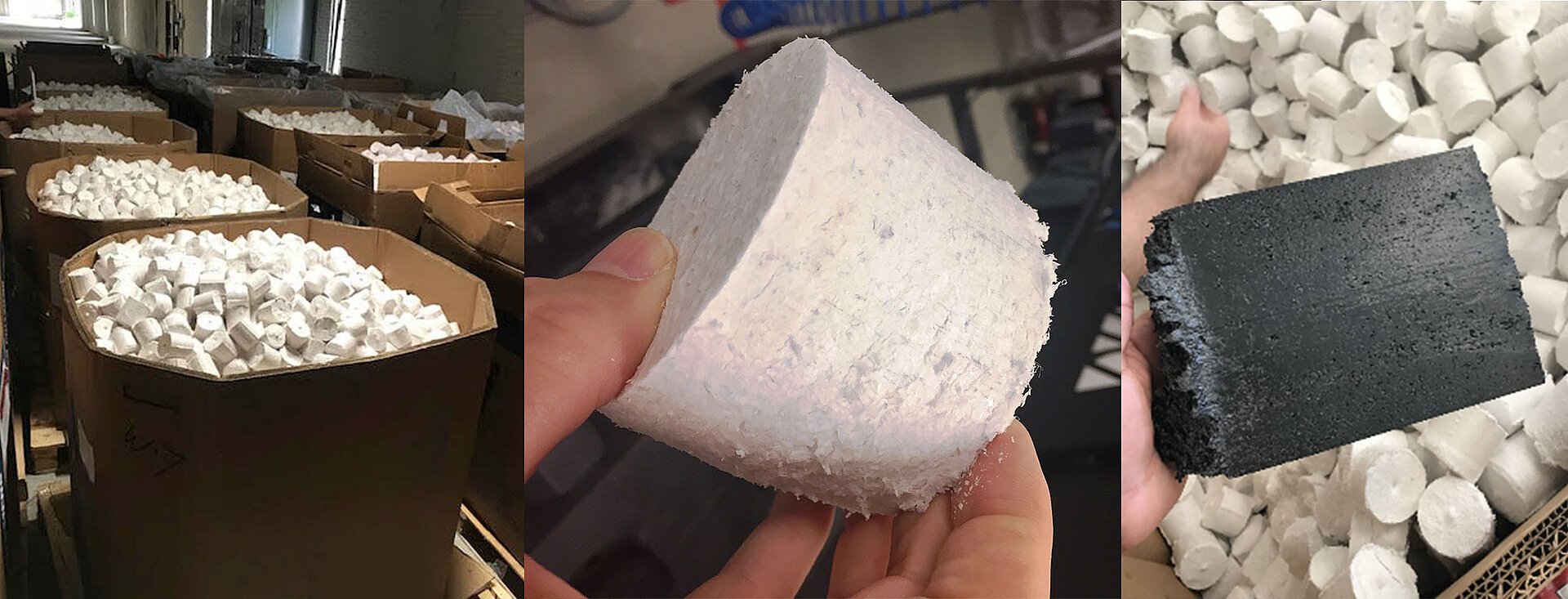
Dans le cadre d'une étude menée dans un grand laboratoire fonctionnant 24 heures sur 24 et 7 jours sur 7 et produisant des substrats vierges mixtes, nous avons observé des économies d'environ 38 % sur la consommation d'eau et de liquide de refroidissement grâce à l'utilisation de systèmes automatisés de gestion des copeaux et du liquide de refroidissement et de micro-séparation, ainsi que d'une presse à briquettes qui compacte les copeaux. Grâce à cette méthode, les copeaux pèsent nettement moins lourd en raison de l'extraction de l'eau, et le volume des déchets est réduit dans un rapport de 12:1.
Enfin, elle augmente également la productivité, car les laboratoires peuvent éliminer l'enlèvement manuel des copeaux à l'étape du surfaçage et accroître leur capacité en réduisant le temps de nettoyage nécessaire.
Devenir plus durable : Une approche à plusieurs niveaux
Pour réduire l'intensité des ressources, une approche à plusieurs niveaux est le moyen le plus prometteur et le plus efficace de devenir plus durable. En commençant par l'optimisation des processus de production pour le rendement et la capacité, en s'appuyant sur des équipements efficaces utilisant des technologies vertes. En outre, l'automatisation intelligente assure un flux fluide et flexible, et même la gestion écologique des bâtiments sont d'excellents moyens de devenir plus durable sans sacrifier l'efficacité économique. D'autre part, l'utilisation de méthodes de production allégées, de l'automatisation et de machines modernes pour améliorer la flexibilité, le rendement et la productivité contribuera même à la rentabilité du laboratoire.
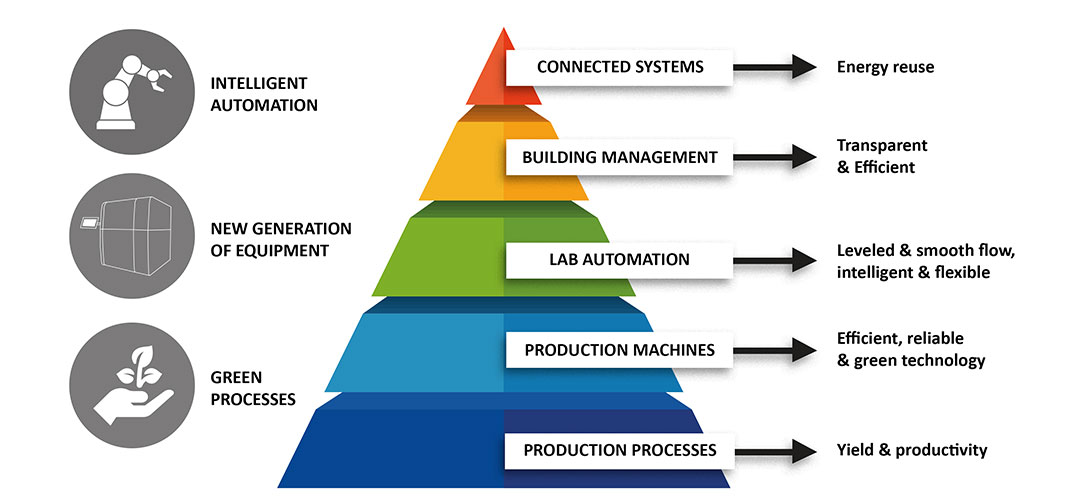
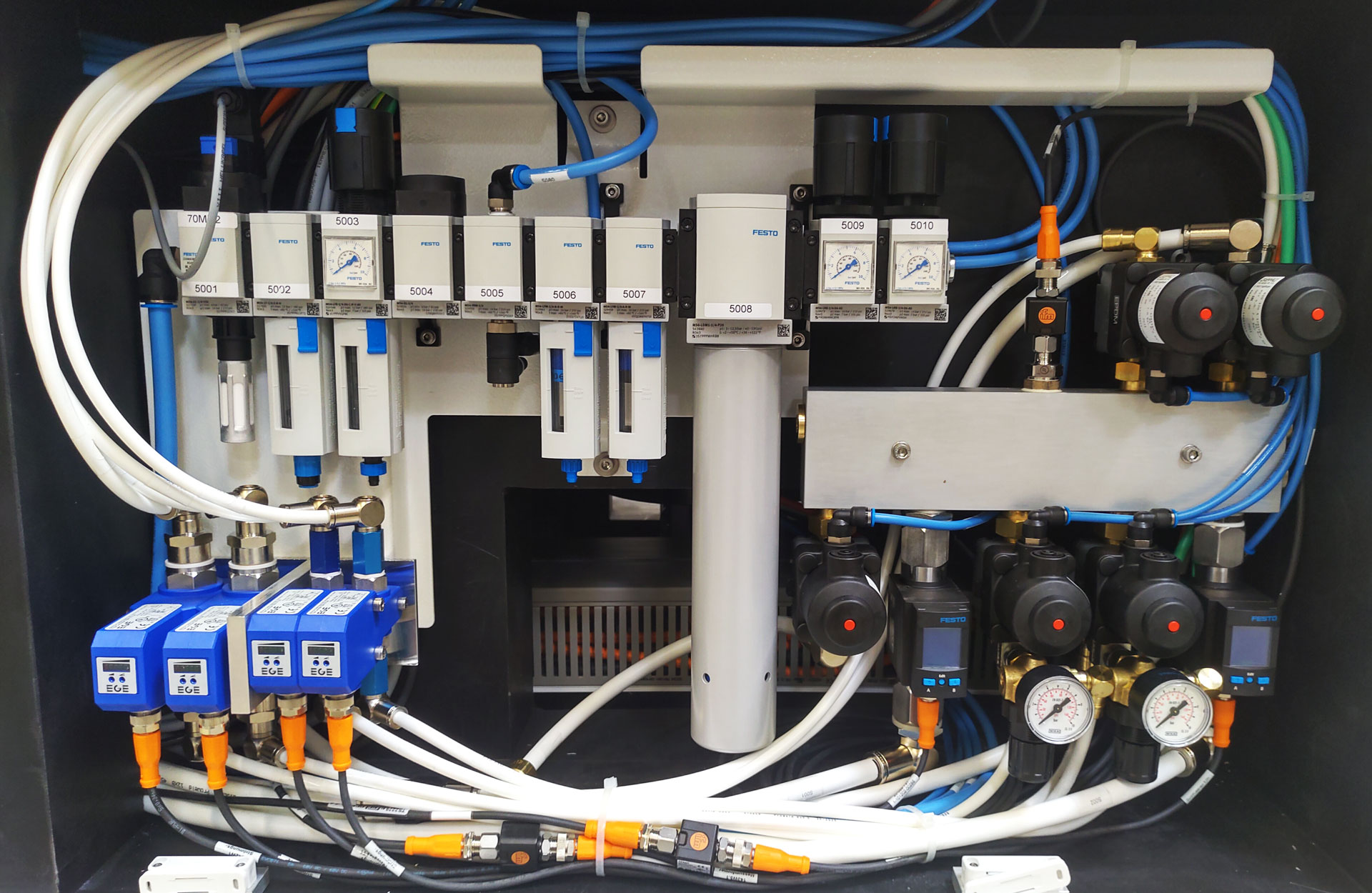
Des machines intelligentes garantissant un rendement maximal pour minimiser le gaspillage d'énergie
Pourquoi une approche de production allégée est-elle si importante ? Les déchets ne sont pas seulement des produits physiques ; ce sont aussi des mouvements non essentiels, des processus redondants et du temps perdu à attendre, ce qui diminue la productivité et, par conséquent, gaspille une énergie précieuse. Le maintien d'une philosophie de production allégée stimulera l'éco-efficacité et l'application de ces principes de production permettra aux laboratoires de contrôler la consommation des ressources.
Le rendement et le temps de fonctionnement sont essentiels, car l'efficacité et l'intensité des ressources sont définies par l'apport de ressources par produit fini. Cependant, si une machine est allumée et maintenue à une température stable, sans débit, de précieuses ressources énergétiques sont gaspillées. Le rendement est crucial, car le rebut est un double gaspillage et une double consommation. L'utilisation des technologies les plus récentes avec des machines intelligentes permet à un laboratoire de contrôler ces paramètres pour une efficacité maximale.
Les machines intelligentes surveillent en permanence les conditions et les indicateurs de performance, ce qui permet une maintenance prédictive, conditionnelle ou automatique. Le suivi de la maintenance des machines est un autre moyen de garantir la disponibilité de la production et des performances maximales. Les machines intelligentes utilisent la maintenance conditionnelle, qui surveille les indicateurs montrant des signes de baisse de performance, ainsi que l'auto-entretien, où la surveillance des conditions et des indicateurs de performance permet à la machine d'auto-ajuster ses processus.
La maintenance conditionnelle et l'auto-entretien contribueront à renforcer le temps de fonctionnement et à gérer efficacement les temps d'arrêt en utilisant des capteurs et en recourant à des logiques internes pour réduire les pannes et optimiser le rendement. Elle aide les laboratoires à réduire les déchets et à devenir ainsi plus éco-efficaces. Des données pour une utilisation optimale des machines Le bon sens, l'expérience et une méthodologie de production allégée permettent certainement d'atteindre un niveau très raisonnable de qualité, de rendement et de temps de fonctionnement, et donc d'éco-efficacité. Pour pousser les performances des opérations de laboratoire au maximum, nous devons nous intéresser à l'IdO, au big data et aux systèmes en temps réel. Comme Peter Sondergaard l'a déclaré en 2011 en tant que SVP chez Gartner, "l'information est le pétrole du 21e siècle" : "L'information est le pétrole du 21e siècle, et l'analytique est le moteur de combustion."
Investir dans des machines prêtes pour Lab 4.0 permettra de réduire la main-d'œuvre, d'être plus rentable, de fournir des livraisons plus rapides, d'avoir moins de casse, d'avoir une empreinte plus petite par travail et de consommer moins d'énergie.
Chaque processus de fabrication génère des données précieuses. Cependant, comme nous l'avons appris, les données seules ne signifient rien - elles deviennent précieuses lorsqu'elles sont affinées par un système d'exécution de la fabrication (MES), qui traduit les données brutes en informations utilisables. Un MES, tel que le MES-360 de Satisloh, permet aux fabricants de prendre des décisions plus intelligentes et, en retour, l'entreprise devient plus efficace dans son ensemble et donc plus rentable.
La mise en place de règles dynamiques pour fermer la boucle de contrôle signifie que lorsque le système détecte qu'une machine ne peut pas traiter un certain objectif, le MES réachemine ces travaux uniquement vers les machines qui ont cette capacité. Par conséquent, la mise en œuvre du système MES contribuera à rationaliser la production en assurant une utilisation optimale des machines disponibles et en améliorant la flexibilité et la productivité. Il garantira un débit et des délais de livraison plus rapides, ainsi que des coûts d'outillage moins élevés, car les tâches sont acheminées vers des machines spécifiques optimisées pour elles.
L'optimisation des ruptures grâce au système MES permet de réduire les déchets. L'analyse des données saisies dans le système MES permet aux fabricants de verres de rattacher les problèmes à des machines spécifiques, à des matériaux de verres, à des ordonnances ou à d'autres facteurs. Les laboratoires peuvent ainsi réagir plus rapidement en cas d'alerte de casse, et les informations sont utilisées pour l'acheminement dynamique des travaux, ce qui se traduit par des rendements plus élevés et des coûts plus faibles, tout en augmentant l'éco-efficacité.
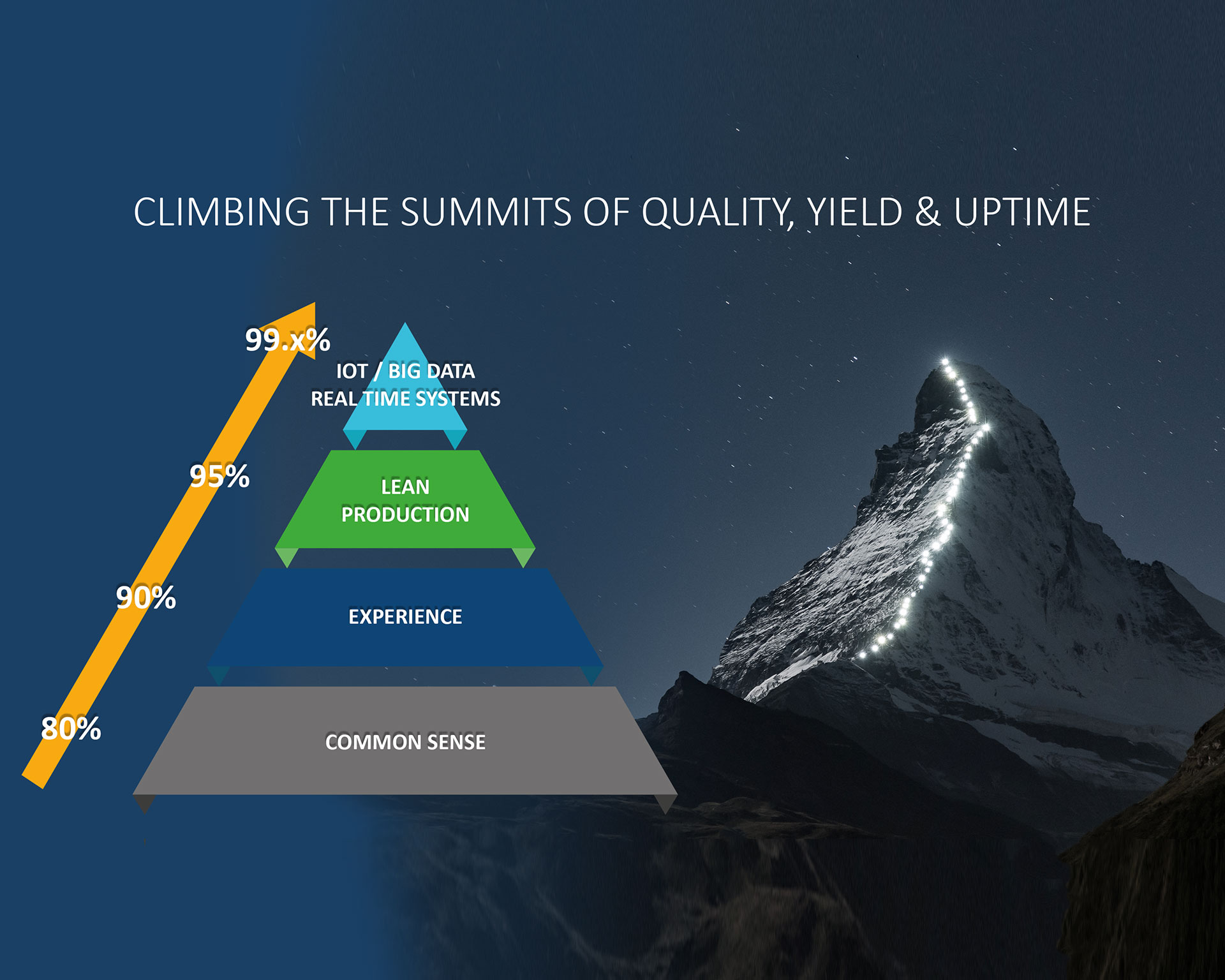
Durabilité 4.0 grâce à une fabrication de verres éco-efficace
Veiller à ce que les laboratoires produisent des verres avec la plus grande éco-efficacité possible signifie réduire les déchets, la consommation d'eau et d'énergie grâce à des processus optimisés qui offrent un excellent débit, un rendement élevé et un temps de fonctionnement optimal. L'association de données et d'une automatisation intelligente contribuera à éliminer les déchets et à accroître l'efficacité. La transparence totale de la production de verres nécessite un système ouvert au niveau des données, avec des machines connectées grâce à l'IoD.
Chaque machine prête pour Lab 4.0 dans l'atelier de production peut être connectée à un MES, ce qui permet aux fabricants de faire fonctionner leur laboratoire au maximum de ses capacités. Le système se connecte, communique et échange des informations avec toutes les machines du laboratoire, quel que soit le fabricant de la machine - et si vous le souhaitez, même avec la machine à café. L'objectif global est de réduire l'empreinte environnementale du laboratoire et, grâce à des machines intelligentes et à la bonne technologie, nous voyons une opportunité de minimiser le volume des déchets, d'améliorer l'utilisation de l'eau et de réduire la consommation d'énergie - et inévitablement de créer le développement durable 4.0 grâce à la fabrication de verres éco-efficaces. Et tout cela sans sacrifier la rentabilité.
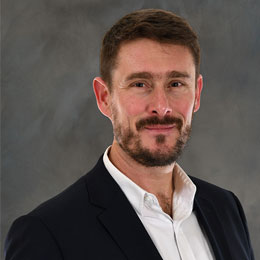
Un article de:
Dr. Michael Kreis
Vice-président de la recherche et du développement au niveau mondial, Groupe Satisloh